Delivering complex plants, such as conveyor plants, requires complex project management because it spans several phases simultaneously, from design to production, and the quantity of inputs to handle is considerable.
The long lead time that a company may face forces it to deliver the plant in different steps, representing the plant areas.
These may also be called Delivery Steps because they are offered at separate moments.
For example, the Manufacturing department is producing and pre-assembling a first Delivery Step; meanwhile, the Engineering department may still work on the final configuration of a second Delivery Step.
With well-coordinated and organized planning, the project can avoid generating extra costs resulting from the repetition of design or manufacturing tasks that could occur, for example, from developing multiple orders to the suppliers for the same products. It’s crucial to consider that executing two phases at different times could result in losing significant information. For instance, the decision to use a specific sensor in a particular area of the conveyor line could be overlooked.
Challenges
Creating a solid process that supports a conveyor line’s delivery phases
The process should consider several essential aspects, such as:
- A guided configuration of the entire plant to design the lines within the spaces of the possible engineered or pre-engineered solutions (ensuring also ETO – Engineering-To-Order – requests)
- The reuse and modularization of the plant and its components to promote the standardization of the products and the reduction of custom parts
- Anticipating the production of the long-lead items, such as the roller pins, to shorten the delivery
- Ensure the consistency of the data and the information exchanged between the people participating in the project
In addition, creating a digital model of the conveyor modules (for example, 3D CAD models) may increase the value of the delivery the company offers to its customers and simplify the design of the products.
Solution
Speed up and keep control over the entire process
Our team, in collaboration with our partners, propose a solution that manages the stages of a plant delivery and the configuration of conveyors in Teamcenter.
Starting from the output of a layout configurator file, we use Rulestream to generate the Teamcenter structure and configure the conveyor automatically.
Process description
- Activity A1 (Layout configuration) gets the customer’s requirements in input and, using the company’s layout configurator produces an XML that includes Layout and project information, focusing on the delivery steps since they are the project billable milestones. The understanding of the layout and the project revision rules drive the activity.
- Activity A2 (Project creation/revision – Delivery Steps Configuration) is assisted by the Rulestream web interface. Based on a classification search, it automatically creates or revises project-specific items like Project items, Delivery Step items, Position items, and Product items. Results are saved automatically in Teamcenter. The activity is driven by the knowledge of the company’s revision rules and the project engineering expertise. The outputs are the details of every module configuration (to drive the CAD), the project structure saved into Teamcenter, and a list of the long lead items that must be put into production as soon as possible.
- Activity A3 (Conveyor CAD Configuration) starts after the modules have been configured and needed modules have not been found in Teamcenter (classification search). The Rulestream Unattended module automatically drives the CAD software to generate the new module assemblies, which are eventually saved in Teamcenter and added to the project structure as children of the Product Items.
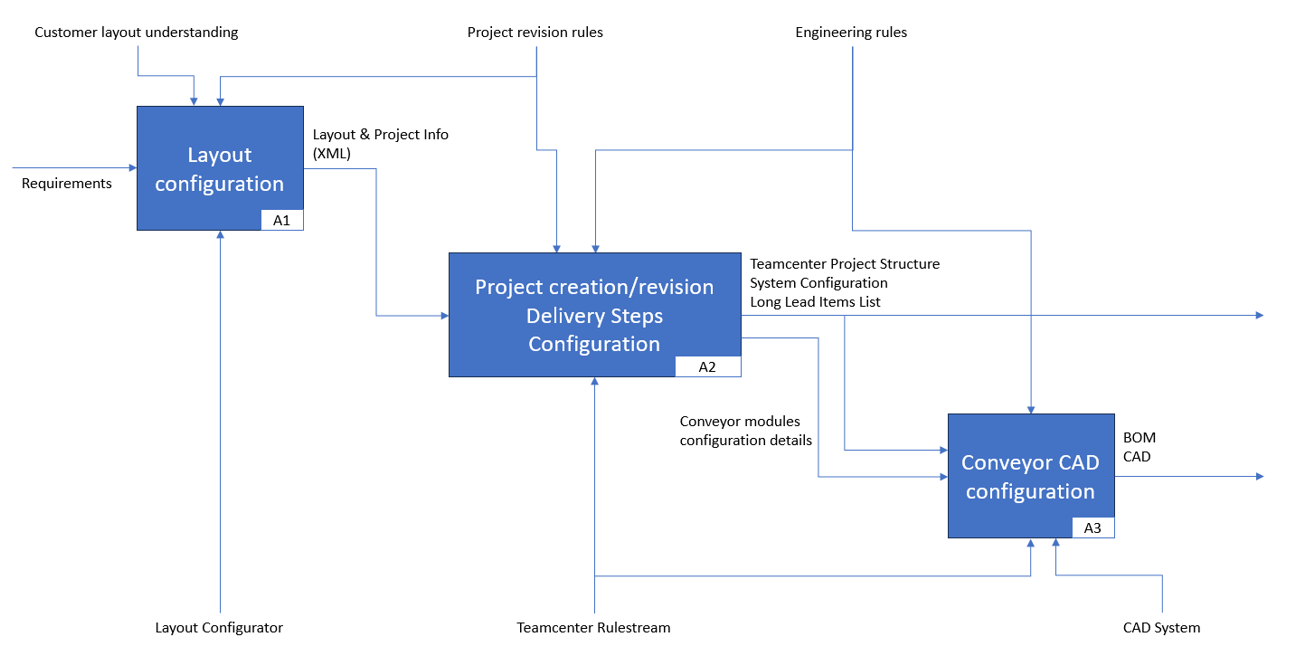